Contribute to the advancement of technology in the metallurgy sector.
Contributing to the search for new machining techniques, AAMS has conducted several studies demonstrating the effectiveness of the methods used:
Case study 1
Context :
Deep hole drilling = high pressure pumps usage – automotive sector.
Objective :
Convert to MQL drilling – energy saving.
Methods :
1- Select optimum tools on market
2- Define MQL parameter (oil variant + up to 10 bars)
3- Proof of concept
4- Tool life test
Conclusions :
MQL suitable
Energy saved
ISO tool life MQL VS Wet
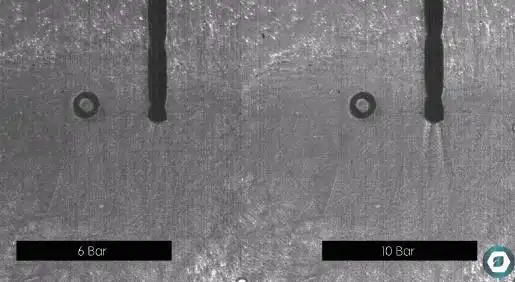
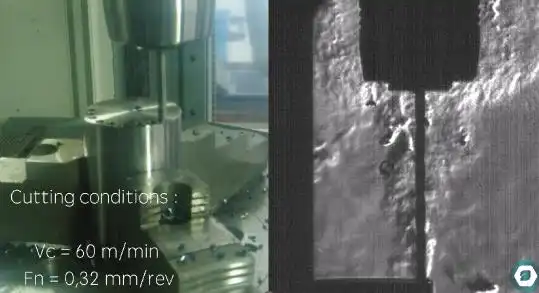
Case study 2
Context :
Consortium project – end user, oil provider – aerospace materials.
Objective :
Evaluation of tool life using 5 wet variants.
Methods :
1- Tool life testing protocol definition
2- Oil benchmark tool life test (3 repeats)
3- Tool wear analysis
Conclusions :
Up to 30% tool life difference
Tool costs decrease
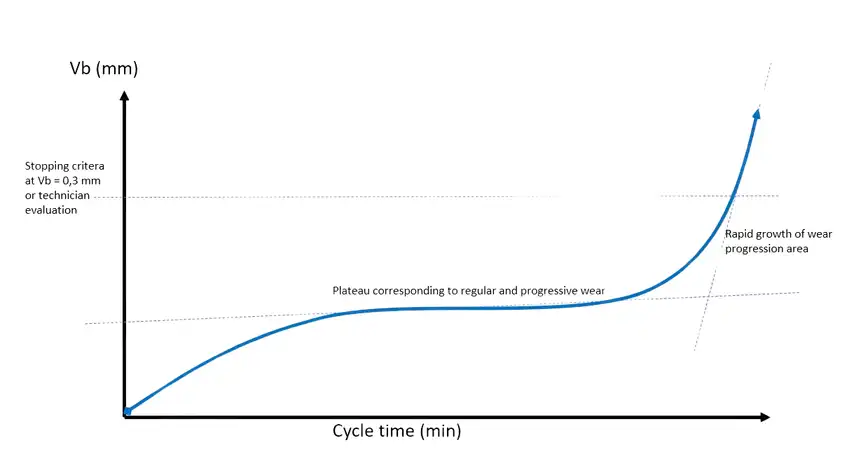
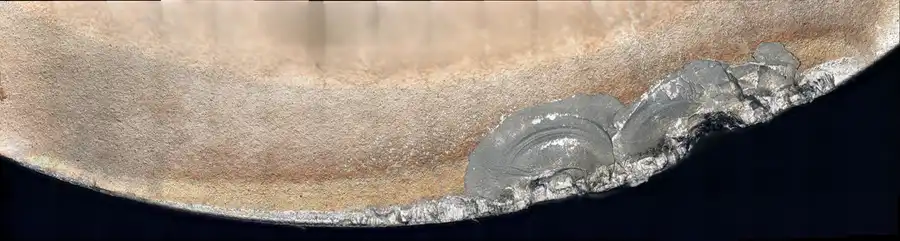
Case study 3
Context :
End user anticipating production growth in medical sector.
Objective :
Audit of production unit and improve productivity.
Methods :
1- One day audit of production unit and actions plan
2- Test performed on production site
3- Delivery of machinability maps using DOE technics
4- Production parameters change + follow-up
Conclusions :
Up to 40% productivity gain.

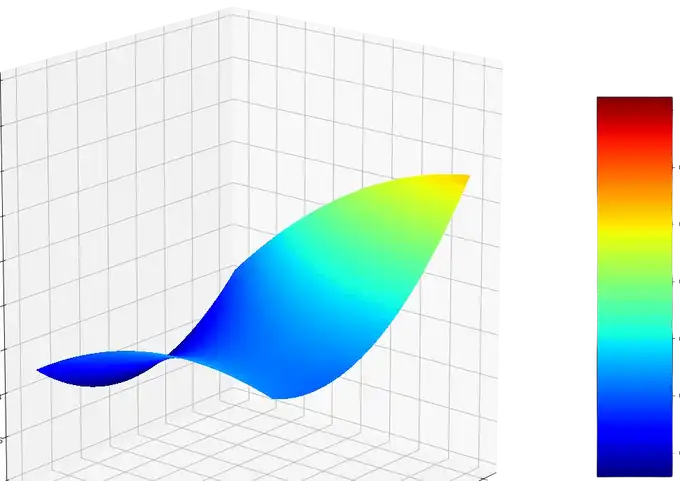
Case study 4
Context :
Consortium projet (Tool manufacturer, University, AAMS).
Objective :
Evaluate friction coefficient and thermal contribution of an AlTiSiN coating in order to find cutting solution for Gamma-TiAl alloys.
Methods :
1- Testing strategy using DOE
2- Usage of a high speed and high pressure pin and cylinder set-up
3- Testing of Ti-6Al-4V alloy versus Gamma TiAl in dry/wet and MQL lubrication condition
4- Measurement of sliding forces and heat flux through pin
Conclusions :
Creation of coating friction map knowledge package for consortium.
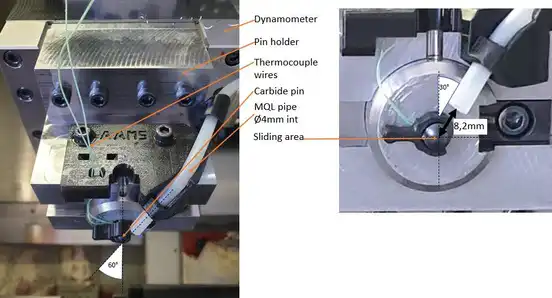
Case study 6
Context :
consortium project (end user, material and tools provider– aerospace market).
Objective :
Mechanical test specimen manufacturing.
Methods :
1- Manufacturing process creation
2- Specimen manufacturing
3- During manufacturing recording of :
• Specimen T°C and heat flux load history
• Specimen mechanical load history
• Specimen vibrations load history
• Specimen roughness 3D map
Conclusions :
Qualification of new machining process.
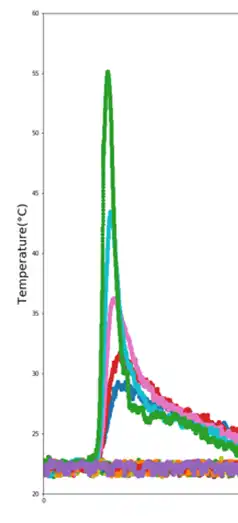
