Equipment and services dedicated to the innovations of tomorrow.
AAMS offers services and solutions.
Solutions to increase sustainability of your process.
Solutions to increase quality of your process.
Solutions to enhance your skills.
We support you throughout the entire process.
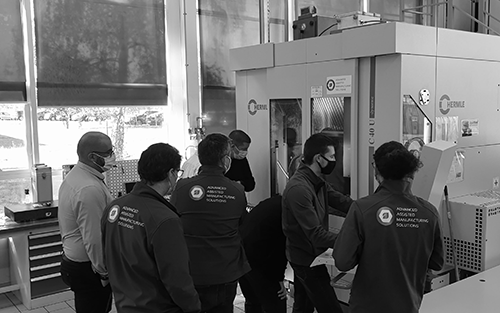
Advice and support
AAMS supports our clients in managing machining production flows while studying optimal technologies and conditions to improve their competitiveness.
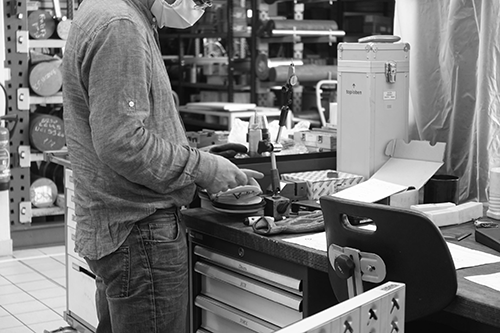
Training in best practices
We help you understand the processes in place to optimize machining production, analyze tool wear, and program CAD/CAM, providing us with the opportunity to share best practices with you. Our training
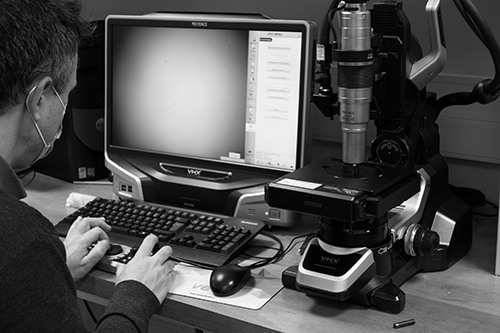
Qualitative measurements
Post-machining measurements are carried out on roughness, residual stresses, and hardness (including nanoindentation for material health composite or metallic). We also perform a microstructural analysis of materials before and after machining.
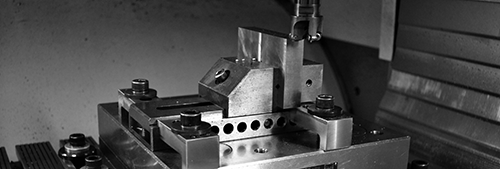
Characterization testing
Implement fatigue testing on various materials: tensile/compression cycling, four-point bending, with the possibility of high-temperature fatigue testing (1500°C).
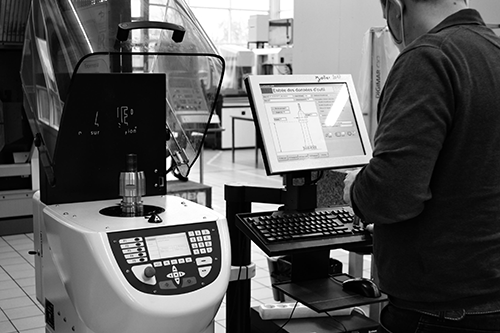
Performance evaluation
Machined surface roughness, three-dimensional measurements, finishing of parts produced by additive manufacturing (expertise in titanium and Inconel materials), support in the design of metallic additive parts.
– 24 000 rpm
– Pmax 40% ED (24kW)
– Axis travel (X/Y/Z): 850/700/500 mm
– Axis movement speed: 60 m/min
– Linear acceleration: 10 m/s²
– Workpiece clamping surface: Ø800 mm
– Spindle type: Capot C5
– CNC: Heidenhain ITC530
– Lubricants used: Internal single-channel MQL via SKF bench (multi-oil)
– Emulsion: adjustable from 10 to 80 bar
– 24,000 rpm
– Pmax S6 60% ED ts 2min (46kW)
– Axis travel (X/Y/Z): 700/600/550 mm
– Axis movement speed: 60 m/min
– Linear acceleration: 10 m/s²
– Maximum axis force: 5000 N
– Workpiece clamping surface: 630 mm
– Spindle type: HSK63
– CNC: SIEMENS 840D
– Lubricants used:
External/internal single-channel MQL VOGEL
– Emulsion: adjustable from 10 to 90 bar
– Tension-compression cycles in two modes: Load – Temperature / Time – Displacement – Temperature
– Maximum load: 3 kN
– Temperature up to 1500°C (ramp 200°C/s)
– Analysis of physical and mechanical priorities (coupling load temperature or displacement temperature)
– STRESS MEASUREMENT SYSTEM BY DIFFRACTION
– Measurement of residual stresses on materials such as: Iron (ferritic, austenitic structures), Aluminum, Titanium alloys, Copper, Ceramic (Alumina)
– Inconel 625-718
– Maximum admissible weight on table: 5 kg, maximum sample height: 150 mm
– Measurement of residual austenite in steel as well